物流業界は、労働人口の減少や物流量の増加にともない、深刻な人材不足に直面しています。「長時間労働の是正」や「作業負担の軽減」が求められる中、従来の「人力」に依存していては物流業務は限界に達してしまいます。
こうした状況で注目されているのが「AGV(無人搬送車)」です。AGVは24時間365日稼働可能で、人手不足の解消や作業効率の向上、労働環境の改善に貢献します。
そこで今回は、AGVの基本的な仕組みや種類、導入のメリット、選び方のポイントを解説します。
※本記事では、日本国内市場で発信されている物流ロボット業界の一般的な情報を考慮しつつ、ギークプラスの見解も交えながら作成しています。成長過程の業界のため、日々変化する市場の中では情報も絶えず変化するものです。そのため、一部解説内容や言葉の定義について、日本国内市場で発信されている情報とは差異が生じることがありますのでご了承ください。
AGV(無人搬送車)で物流現場が変わる
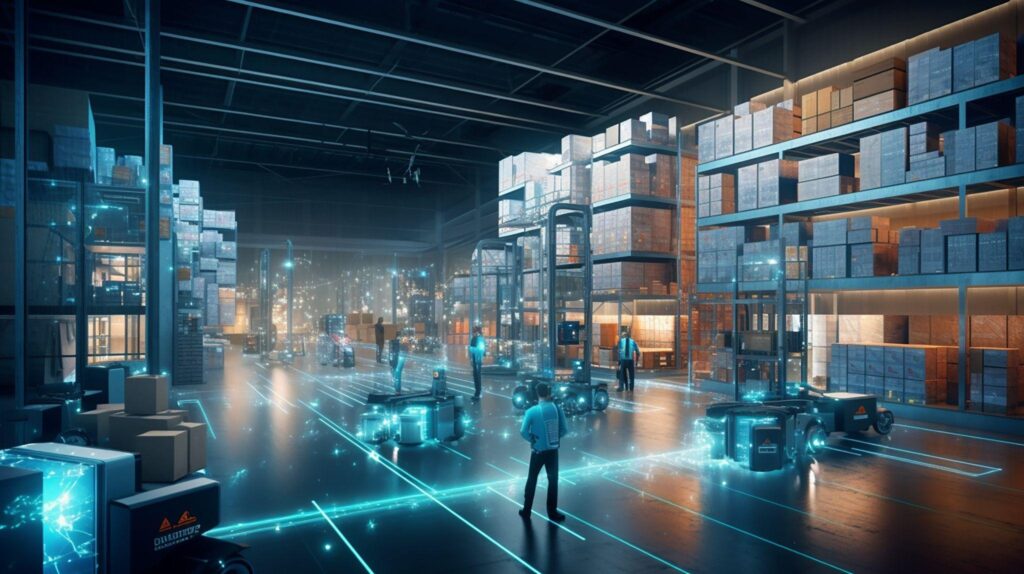
AGVの導入は、物流現場の環境を大きく改善します。人材不足の解消や作業効率の向上、人的ミスの削減など、多くのメリットが期待できます。
物流現場の自動化・省人化を実現する重要な選択肢として、今後ますます注目を集めるAGV。まずは、その基礎知識について見ていきましょう。
AGVとは?
AGVは「自動化された搬送システム」のことで、「無人搬送車」または「無人搬送機」とも呼ばれるものです。
AGVは、材料や部品を所定の場所へ自動で運搬します。従来のコンベヤやフォークリフトに代わる運搬手段として、製造現場を中心に広く活用されています。
主な活用例は以下のとおりです。
- 倉庫での入出庫作業
- 製造ラインでの部品や完成品の搬送
- 病院でのリネンや医療器具の運搬
- 飲食業界での配膳作業
AGVは、特に工場のスマートファクトリー化(AIやIoTを活用して製造プロセスの最適化を図ること)において重要な技術であり、作業の自動化と効率化を推進します。
AGVと類似する無人搬送システムとの違い
AGVと類似するシステムに「AMR(自律走行搬送ロボット)」と「RGV(有軌道式無人搬送台車)」がありますが、それぞれ異なる特徴を持つ無人搬送システムです。
<無人搬送システムの特徴比較>
種類 | 長所 | 短所 |
---|---|---|
AGV | ・比較的低コストで導入可能 ・人的コストの削減が可能 ・走行スピードが速い | ・固定ルートのみの走行 ・即時的なレイアウト変更に柔軟に対応できない |
AMR | ・自律的に最適経路を選択可能 ・障害物を回避して走行可能 | ・AGVと比較して導入コストが高い ・メンテナンスが難しい ・走行スピードが遅い |
RGV | ・レールを通じて給電可能 ・長時間の連続運転が可能 | ・レールの設置が必要 ・走路上に段差が生じる |
無人搬送システムの導入を検討する際は、作業環境やコスト面などを多角的に評価し、最適なシステムを選択することが重要です。物量や拠点のレイアウトによっては、AGVで十分にカバーできる場合も多いでしょう。
AGVの種類と特徴

AGVは、積載型や低床型など、搬送方法や用途に応じてさまざまな種類があります。それぞれが用途に応じた特性を持ち、工場や倉庫での作業の効率化に貢献します。
ここでは、主なAGVの種類と特徴について見ていきましょう。
積載型
積載型AGVは荷物を台車に載せて搬送するAGVのことで、最も基本的で汎用性の高いAGVです。積載型は、台車部分に荷物を直接載せて運ぶため、さまざまな形状やサイズの荷物に柔軟に対応できます。そのため、製造業や物流業だけでなく、商業施設などでも広く利用されています。
積載型AGVを選定する場合は、搬送する物資の重量や大きさ、搬送経路の状況を考慮することが重要です。また、走行経路の確保や荷物の積み下ろし場所の設定など、現場のレイアウトや作業フローの調整が必要な場合もあります。なお、荷物の積み下ろしまで自動化する場合は、積み台にコンベアが搭載されているコンベア型のAGVが必要になります。
棚搬送型
棚搬送型AGVは、主に倉庫や物流センターで使用されるAGVです。棚全体を持ち上げて移動させる能力を持ち、高い収納効率と迅速な商品ピッキングが特徴です。必要な棚を作業者のもとへ自動的に運搬することで、作業者の移動時間を大幅に削減し、ピッキング効率を向上させます。
導入時は既存の倉庫システムや商品管理システムとの連携が重要で、適切に導入することで倉庫業務の効率化と人的ミスの削減を実現できます。
けん引型
けん引型AGVは、大量輸送に優れた特徴を持っています。台車やトレーラーを一度に複数けん引して運搬するため、大規模な工場や物流センターでの運用においては非常に有効です。
けん引する量が増えて長くなるほど曲がり角での内輪差も大きくなるため、導入時には搬送経路の幅や曲がり角の広さ、施設全体のレイアウトとの適合性を十分に確認することが重要です。施設の設計やAGVの運行ルートを最適化することで、最大限の効果を引き出せます。
低床型
低床型AGVは車体が低く設計されたAGVです。パレットや棚の下に潜り込んで荷物を持ち上げて運搬します。これにより、荷物の積み下ろし作業が不要となり、作業時間の短縮が見込めます。工場や倉庫での重量物搬送や既存設備との連携が必要な場面で活躍します。
また、低床型AGVには、異なる高さの荷物に対応できるリフター機能が備わっているものもあります。このタイプはコーナーを曲がる際に曲がり角で一旦停止し、90°回転して再度走行するのが一般的です。そのため、道幅が最小限で済み、省スペースでの運用が可能です。
重量型
重量型AGVは、数十トンから数百トンにも及ぶ荷物を運搬するために設計されています。製造現場や大規模な物流施設などでの需要が高く、その頑丈な構造と高い積載能力が特徴です。
以前はディーゼルで駆動するタイプもありましたが、最近の重量型AGVはバッテリー駆動が一般的で、高度なセンサー技術を搭載し、安全性も確保されています。特に自動車産業や造船業など、非常に大きな部品を扱う業界で重宝されていますが、導入には施設のインフラ対応が必要で、コストも高くなる可能性があります。
屋外型
屋外型AGVは、屋外環境での使用を目的に設計されたAGVです。雨風や直射日光などの厳しい環境下でも安定した運行が可能で、舗装されていない道や凹凸のある路面でも安心して使用できます。
一般的に高性能センサーやパトライトを搭載して安全性が確保されており、無人運転と有人運転の切り替えも可能です。また、重量物の運搬にも対応できる高い積載能力と、GPSによる正確なナビゲーション機能も備えています。
AGV導入のメリット
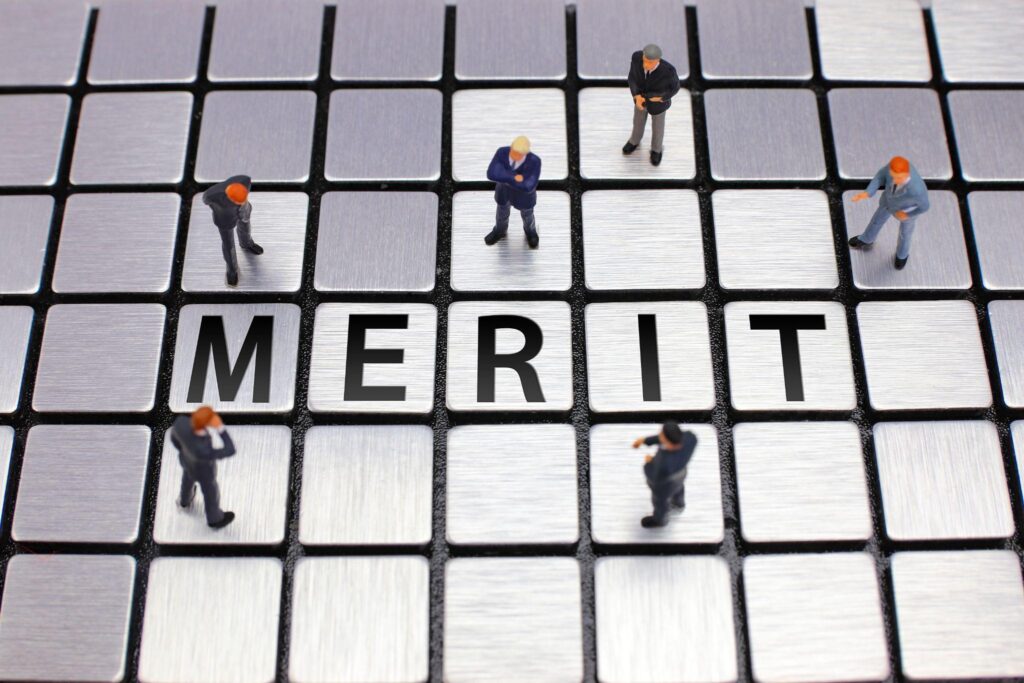
AGVを導入することで、業務効率化など、さまざまなメリットがあります。次に挙げるようなAGVの主なメリットについて解説します。
- 歩行距離の削減
- 人件費の削減
- 労働力不足の解消
- ヒューマンエラーの削減
歩行距離の削減
AGVの導入は、作業員の歩行距離を大幅に削減する効果があります。従来の倉庫作業では、ピッキングや商品運搬のために作業員が広い倉庫内を頻繁に移動する必要がありました。しかし、AGVが商品や棚を作業員のもとへ自動的に運搬することで、この移動の大部分が不要となります。
特に、棚搬送型AGVを導入した場合、作業員はほぼ一箇所に留まってピッキング作業を行うことが可能になります。これにより、作業効率が大幅に向上し、労働負荷も軽減されます。
歩行距離の削減は作業時間の短縮にもつながり生産性の向上に寄与し、後述するヒューマンエラーのリスク低減にも大きく貢献します。
AGV導入による歩行距離の削減は、物流現場の効率化と作業環境の改善に大きく貢献する重要な要素といえるでしょう。
人件費の削減
AGVは、倉庫内でのピッキングや出荷場所への搬送、商品仕分け作業などを自動化するため、人員数の最適化が可能です。その結果、人件費の大幅な削減が期待できます。
また、AGVの導入によるメリットは単なる労働コストの削減にとどまりません。労働力不足解消のための人材の募集や採用にかかる経費、新人教育にともなう時間的および金銭的負担も大幅に軽減できます。
熟練スタッフが教育に費やす時間も減り、自身の業務に専念できるため、間接的なコスト削減にもつながるでしょう。
AGVの導入には初期投資が必要です。しかし、長期的にはコスト削減につながり、労働人口の減少が進む中で、将来的な人件費の上昇リスクを緩和する効果が期待できます。
労働力不足の解消
AGVは、24時間絶え間なく稼働することが可能です。よって、人による夜間作業や残業の負担が軽減され、人的資源を他の重要な業務に効率的に配置することが可能です。
加えて、AGVは従業員の肉体的な負担を大幅に軽減します。単調な搬送作業をAGVが代行することで、従業員はより重要な業務に集中できるようになります。
また、労働環境の改善により、従業員の仕事に対する満足度を高め、結果として離職率の低下といった副次的な効果も期待できるでしょう。
ヒューマンエラーの削減
AGVは、あらかじめプログラムされたとおりに動作するため、人間が陥りやすい判断ミスや勘違いによるエラーを回避できます。特にピッキング作業では、商品の取り違えといった基本的なミスを防ぎ、品質管理を大きく改善することが可能です。
さらに、AGVは機械であることから人間のように疲労の影響を受けないため、長時間労働や単調な作業でも安定した動作を維持でき、ミスのリスクを大幅に減少できます。
ヒューマンエラーの削減は、顧客満足度の向上にも直結します。出荷ミスや数量の間違いが減少することで、顧客からのクレーム件数が減少、引いては企業の信頼性が高まってブランド価値の向上が期待できるでしょう。
AGV導入のデメリット
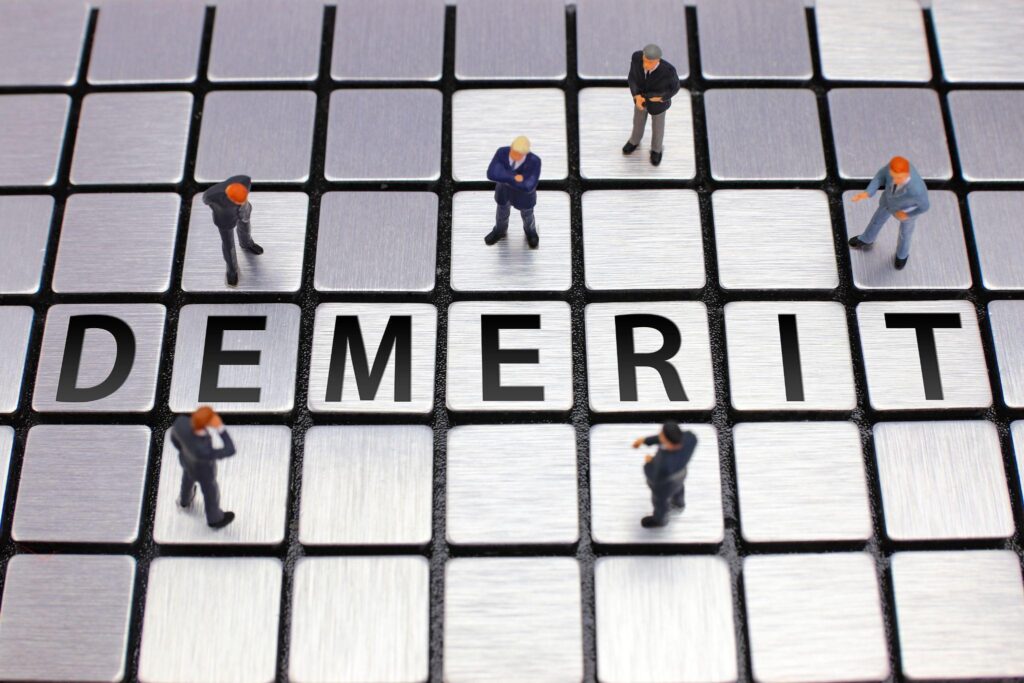
多くの導入メリットがあるAGVですが、次に挙げるようなデメリットもあります。
- 初期投資とランニングコスト
- AGV導入時の現場環境の課題
これらのデメリットや課題を理解し、適切な計画と対策を講じなければ、AGV導入の成功にはつながりません。それぞれ詳しく見ていきましょう。
初期投資とランニングコスト
AGVの導入には、一般的に初期投資が必要です。主な費用は、AGV本体の購入費や搬送路の整備、誘導システムの設置、作業レイアウトの再配置などが挙げられます。
また、運用に必要なソフトウェアやシステムの統合にかかる費用、定期的な保守点検や電力などのランニングコストも無視できません。
これらの費用は、導入するAGVのタイプや台数、使用頻度、運用する場所の条件によって大きく変動します。特に中小企業にとっては、これらすべての費用を賄うことが大きな経済的負担になる可能性があります。
しかし、長期的には労働コストの削減や生産効率の向上など、費用対効果が期待でき、他のシステムや機器との連携を図ることで、投資効果の最大化が可能です。
AGV導入時の現場環境の課題
AGVの導入には、まず搬送経路の最適化が不可欠です。具体的には、通路の幅や入口、ルート上の障害物などを確認し、状況に応じてレイアウトを変更する必要があります。この過程で一時的に業務が停滞する可能性もあるため、詳細な計画を立て、段階的に導入するのも方法の一つです。
また、AGV導入は既存の業務フローが大きく変わることが予測されるため、従業員に対する教育とトレーニングが欠かせません。段階的な導入と並行して新しい現場環境についての教育を実施することで、従業員が円滑に適応できるようになります。
さらに、AGVとの接触事故など新たなリスクが発生する可能性もあります。このリスクを最小限に抑えるため、センサーによる障害物検知や警告システムなど安全対策の徹底が必要です。
自社に最適なAGVを選ぶポイント
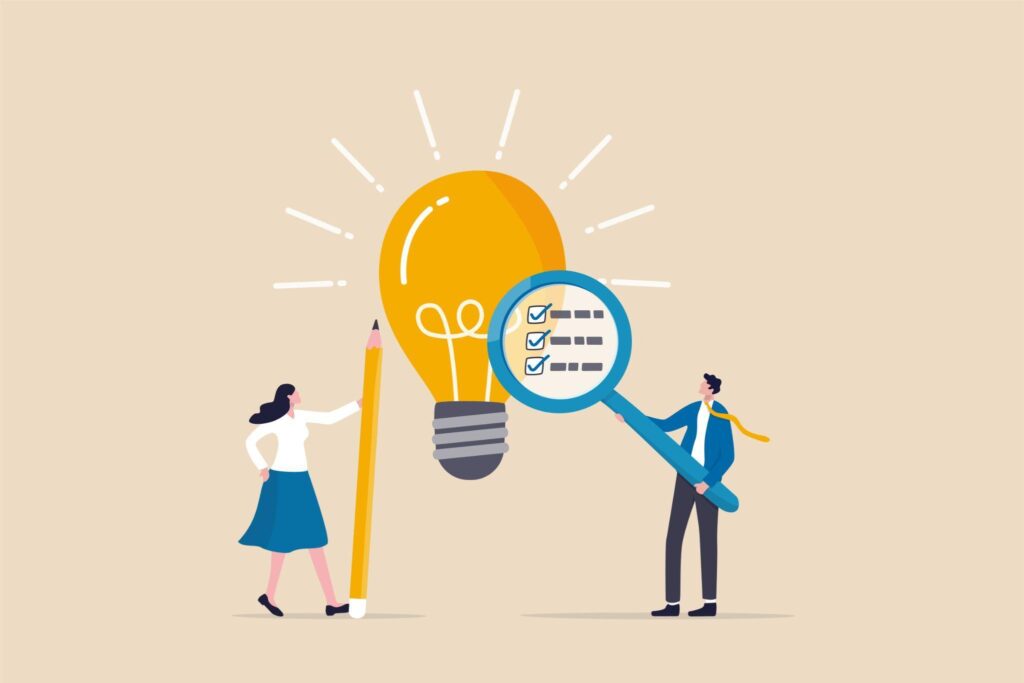
AGV導入を成功させるには、まず自社の現状と直面している課題の分析が不可欠です。その上で、自社の業務フローや作業環境に最も適したAGVを選ぶことが求められます。
最適なAGVを選ぶ際のポイントは、主に次に挙げるような点です。
- 搬送物の種類
- 走行方式
- 現場環境
- 費用対効果
それぞれ詳しく解説します。
搬送物の種類
搬送物の種類に応じて、AGVの選択は大きく変わります。例えば、小型荷物やダンボール、小型コンテナなどを搬送する際には、積載型のAGVが効果的です。一方で、固定棚やパレットをそのまま移動させるには、低床型のAGVが最適です。
それぞれのAGVに適した主な搬送物は次の表のようになります。
<AGVの種類と適した搬送物>
AGVの種類 | 特徴 | 適した搬送物 |
---|---|---|
積載型 | 台車タイプで荷物を直接積載 | 小型荷物、ダンボール、小型コンテナなど |
低床型 | 搬送物の下に潜り込んで持ち上げて搬送 | 固定棚、パレットなど |
けん引型 | 棚ごと引っ張って搬送、複数台連結可能 | 可動棚、かご台車、パレット台車など |
適切なAGVの選定によって、搬送作業の効率化や作業員の負担軽減、搬送ミスの抑制など、全体の業務効率化と信頼性向上につなげることができます。
走行方式
AGVの導入において、どの走行方式を選ぶかは非常に重要です。走行方式と特徴は次のとおりです。
<AGVの走行方式と特徴>
走行方式 | 特徴 |
---|---|
磁気テープ誘導式 | 床に貼付された磁気テープを検知して走行。設置が容易で信頼性が高い。 |
光学誘導式 | 床面の反射テープや色線をカメラで認識。低コストで導入可能。 |
SLAM式 | センサーで周囲を認識し、地図作成と自己位置推定を同時に行う。柔軟な経路設定が可能。 |
2次元コード式 | 床や壁のQRコードを読み取り位置を特定。高精度な位置決めが可能。 |
走行方式は、最終的な効率性やコストに影響を与えるため、現場の特性や必要とされる精度、総合的なコストなどを慎重に検討することが求められます。
現場環境
AGVを導入する際には、現場環境の事前調査が不可欠です。AGVや搬送物のサイズに応じて、通路幅や旋回スペースを適切に設ける必要があります。固定設備が走行を妨げないよう、必要に応じて移動や撤去を行うことも重要です。
また、防火シャッターをまたいだ運用を行う際は、AGVがシャッター下や避難通路をふさがないよう、火災報知器と連動して、停止する際に指定箇所を避けるといった機能が必要になります。
AGVの電子機器は温度や湿度に敏感なため、極端な環境での運用は避ける必要があります。さらに、床面の凹凸や段差、滑りやすい場所は走行精度や安全性に影響を及ぼす可能性があるため、注意が必要です。
こうした要因を包括的に確認して適切な改善策を講じることで、AGVのパフォーマンスを最適化し、導入のメリットを最大限に引き出せるでしょう。
費用対効果
AGVを導入する際には、費用対効果を全体的に評価することが重要です。初期投資にはAGV自体の費用や設置にかかる工事のコストが含まれます。これに加えて、他の装置と連動する場合には、管理システムのカスタマイズ費用も考慮しなければなりません。
運用コストには、消耗品の交換費用や定期メンテナンス、既存設備との連携にかかる費用が発生します。
費用対効果を正確に評価するには、これらの導入・運用コストと合わせて、AGV導入メリットを評価することが大切です。具体的には、人件費削減や作業者の負担軽減、業務効率化によるコスト削減などが挙げられます。
最終的に、これらの要素を総合的に判断し、AGV導入が最適な選択であるかを判断する必要があります。
AGV導入の成功事例と注意点
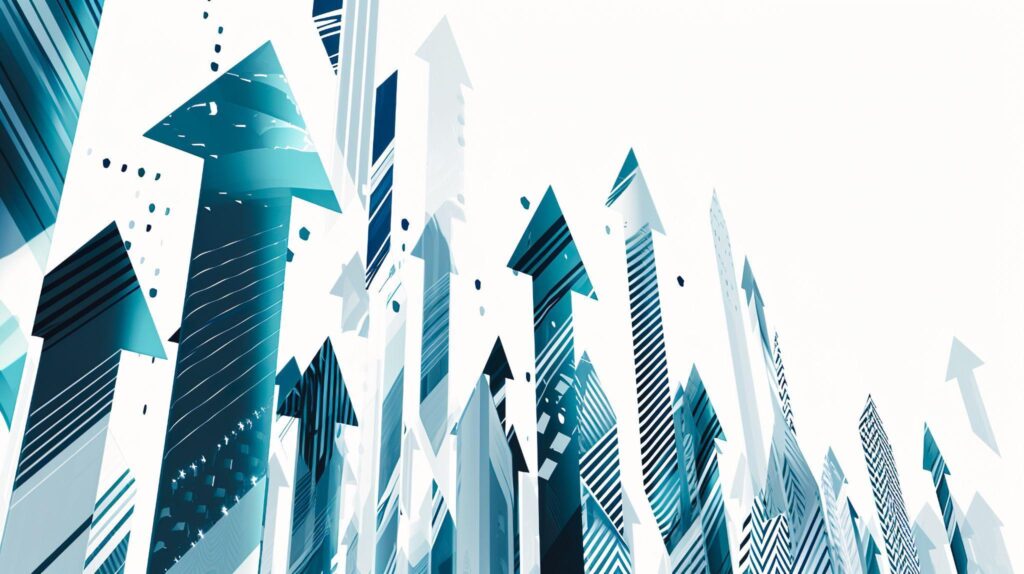
AGVの導入は、多くの業界で生産性向上やコスト削減に貢献しています。しかし、本来の効果を引き出すには、企業のニーズの明確化やインフラ整備など、計画と準備が必要です。
ここでは、AGV導入の成功事例と、導入時の注意ポイントを解説します。
製造業におけるAGV導入事例
Kerry Logisticsは、Dellのスペアパーツ倉庫で、限られた保管スペースと手動ピッキングの低効率という二大問題に直面していました。
課題解決のために、同社はギークプラスのピッキングロボットを32台導入し、2,000台以上の棚を設置するという改革を実行。この施策により、在庫回転効率が10倍に向上し、倉庫スペースを最大限に活用可能となりました。
また、作業員数を減らしつつも作業効率とピッキング精度の向上が実現し、人件費や管理費の削減効果も得られました。
この事例は、製造業界が自動化技術を活用することにより、作業の効率化と生産性の向上を実現できることを示しています。
■詳しくは以下の関連ページでもご紹介しています。
なぜDellはギークプラスのピッキングソリューションを選んだのか?
物流倉庫でのAGV導入事例
アルペンは、急速に拡大するEC市場に対応するため、2018年に物流拠点をプロロジスパーク千葉ニュータウンに移しました。
しかし、リードタイムの短縮や人手不足といった課題が浮上。この状況を打破するため、AGVの導入を決定し、2018年から2021年までの間に段階的に導入を進めました。まず2018年にピッキングロボット56台・棚約1,000台を導入し、2020年にはピッキングロボット40台を追加、そして2021年にはさらにピッキングロボット120台・棚約1,200台を導入しました。
この結果、ピッキング作業の効率は従来の手作業に比べて約3倍に向上し、保管と出庫の能力はそれぞれ2倍と3倍に伸びました。AGVの導入は、アルペンの物流戦略において極めて重要な役割を果たし、長期的なビジネス成功への大きな一歩となりました。
■詳しくは以下の関連ページでもご紹介しています。
【アルペン】 ロボットの段階的拡張により、年々拡大するEC需要に対応 | Geek+
AGV導入時のよくある失敗から見る注意点
成功事例とは反対に、AGV導入の際によくある失敗のポイントを整理してみましょう。失敗の原因を把握することで、導入時に注意すべき点が見えてきます。
ここでは、計画段階、実際の運用、長期的視点、投資に対する費用対効果の4つに分けて簡単にご紹介します。
<AGV導入時のよくある失敗>
失敗のポイント | 失敗の要因例 |
---|---|
計画段階 | 運搬する物品の特性を正確に理解していない |
運用段階 | 従業員への教育不足や、AGVメーカー・販売会社によるサポート不足 |
長期的視点 | システムの拡張性や他のシステムとの連携が不十分 |
費用対効果 | すべての問題が重なり運用コストが増加 |
失敗のリスクを避けるためには、計画段階からしっかりとした検討を行い、長期的な視点を持つことが重要です。
冒頭でも触れたとおり、AGVと類似する無人搬送システムにAMRやRGVなどがありますが、それらの特徴を理解せずに導入しても想定していた効果が得られない場合があります。また、将来的な拡張を考慮せずにシステムを作り込んでしまうと、拡張が必要なときに作業が難航し、莫大なコストが発生する可能性もあります。
特に自社に知見がない場合には、運用実績と優れた専門知識を持つ外部サポートの活用が、成功への大きな助けとなるでしょう。
なお、AGVは導入後も稼働状況の検証などを行い、生産性向上のためのアップデートを重ねていくことが重要です。しかし、AGVを「売って終わり」にしてしまうメーカーや販売会社も多いのが現状で、導入後の運用改善に関するサポートが得られず、AGV導入が失敗に終わるケースも散見されるため注意が必要です。
日本国内市場の物流ロボットに関する情報の誤解と、正しい導入効果のポイント
日本国内での物流ロボット導入が進む中、AGVやAMRの定義や導入効果に関して、誤解とも言える情報が広がっています。特にAMRは、新しい技術として注目される一方で、実際の導入効果や可能性が十分に理解されていないケースも見られます。
例えば、次に挙げるような情報は、日本国内市場における誤解とも言える代表的な情報です。
AGVは古い技術であり、AMRはすべての面で優れているという誤解
AMRは新しい技術とされていますが、AGVも進化しており、用途に応じて適した選択が必要です。
AGVはガイド設置が必須で、自律走行もできないという誤解
AGVには従来型のガイド設置が不要なものもあり、また、自律走行が可能なものもあります。日本国内市場でAMRにカテゴライズされているものだけが自律走行型というわけわけではありません。
AMRが導入されれば、生産性が大幅に向上するという誤解
AMRの導入は効果的ですが、必ずしも全ての環境で生産性向上が見込めるわけではありません。人とロボットとの作業領域が共存することで、かえって生産性が低下する場合もあります。
AMRは初期投資が高いが、長期的には必ずコスト削減につながるという誤解
実際には、メンテナンスコストや運用環境により、必ずしもコスト削減に直結しないケースもあります。
AMRの導入が進めば、人手不足の問題が解決するという誤解
AMRが人の作業を補助することで効率化は図れますが、完全に人手が不要になるわけではなく、適切な人員配置が依然として重要です。
日本国内市場では「自律走行できる方式=AMR」という定義が定着してきましたが、ギークプラスのAGV製品のように、自律走行も可能で柔軟性を備えたAGVもあります。そのため、単純に「AGVはガイドが必要で自律走行ができない」と決めつけると、誤ったビジネス判断をしてしまうことにもなりかねません。
国内市場で事業展開する各社によって異なる言葉の定義があることを認識し、その自動搬送ロボットがどのような機能や特徴を備えているのかを、正しく理解することが重要です。
詳しくは下記の記事で詳しく解説していますので合わせてご覧ください。
【関連記事】
物流ロボット(AGV・AMR)の活用・導入効果を正しく理解するためのポイント~国内市場で散見される誤解
AGVが変える現場の未来
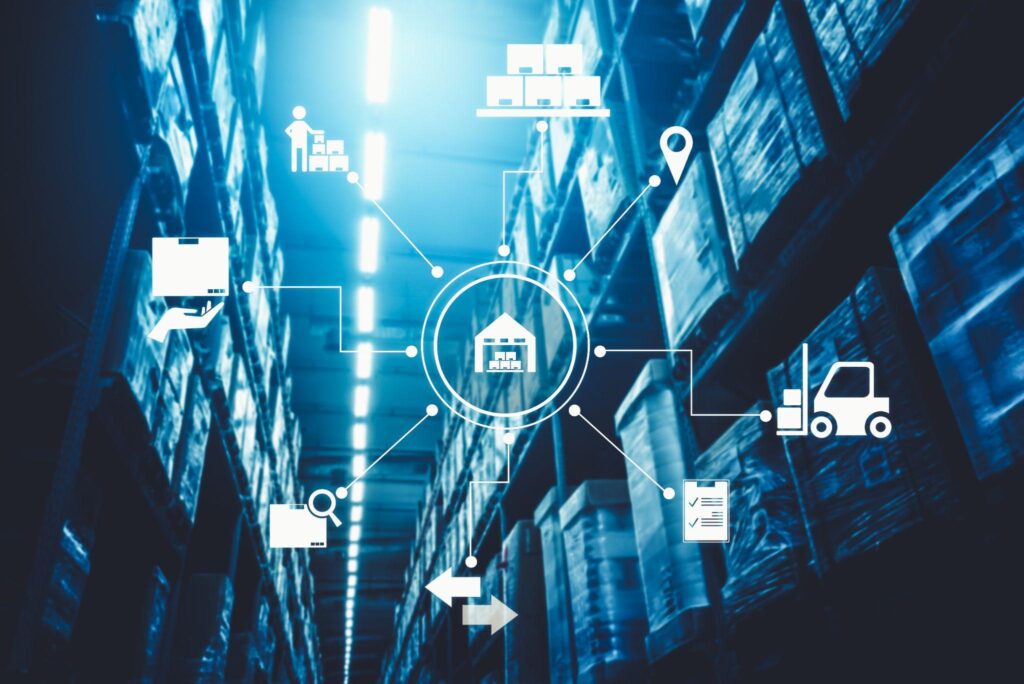
AGVは、物流業界において業務効率化や人件費削減を実現するといったメリットがあります。しかし、導入費用やランニングコスト、運用に必要な専門知識の習得という課題も存在します。
これらの問題への解決策として注目されているのが、ギークプラスが提供する「Logistics as a Service(LaaS)」です。
LaaSでは、EC物流のオートメーション化に必要なハードウェアとソフトウェアを、初期費用ゼロの従量課金型モデルで提供します。また、ロボットの実稼働現場での実習や座学を通じたノウハウのサポートを受けられるといった特徴もあります。これにより、中小企業でも手軽に物流の自動化を実現することが可能です。
AGVのメリットと課題をしっかりと認識し、LaaSのような新しいソリューションを活用することで、物流業界における自動化の効果を最大限に発揮できるでしょう。